From broom to sweeper
The sweeping principles through the ages
We have been developing and manufacturing vacuum sweepers for over 40 years.
The widely used single roller technology of the time was replaced by the revolutionary tandem roller system developed by Stolzenberg. This innovative TRS sweeping technology is used in almost all Stolzenberg sweepers.
All the disadvantages of the older technologies have been eliminated and a previously unrivalled level of efficiency has been achieved.
Here you will find an overview of the sweeping technologies once used and further developed by Stolzenberg, as well as newly invented and revolutionary sweeping technologies.
Even the early days of the sweeping technology world made new brooms look old on large surfaces. Founded in 1889 as a brush factory, Stolzenberg has been active in the development and production of hand-operated sweepers for over 40 years. In 1965, when the mainstay "carpet sweeper" had to give way to the booming market for household hoovers, an attempt was made to develop an "enlarged carpet sweeper" for industrial cleaning. What was initially used for the company's own needs soon met with great interest from buyers and therefore went into series production. How the first German sweepers worked: the so-called dustpan principle.
The problem of the dustpan principle
The rear sweeping roller rotates against the direction of travel of the sweeper when moving forwards. When driving over the dirt, it has to pass under a rubber lip in order to be swept into the dirt container at the front like a kind of dustpan. In practice, however, this first development step harbours some problems.
Problem Area
Due to the necessity of attaching a support wheel at the front of the machine, it always operates in the unswept area. As a result, larger debris particles can block the operation of the sweeper.
Problem Area 2
Due to the front-positioned waste container, all debris must first pass through this "bottleneck." This significantly limits the size of debris that can be collected.
Problem Area 3
The dustpan-like incline, over which debris is swept, must not exceed a certain ground clearance to ensure that the debris reaches the container. As a result, the filling volume is significantly limited, because once the collected debris surpasses the edge, it falls back toward the roller.
Problem Area 4
A rubber lip, under which debris must pass to be picked up by the sweeping roller, prevents lighter materials such as paper or dry leaves, especially on smooth surfaces, from being effectively collected.
The numerous shortcomings of this very simple sweeping principle necessitated further development. As a result, the single-roller throw-over technique was developed, though exclusively for motorized sweepers.
Roll-in throw-over system
The further development of the sweeper
The numerous shortcomings of the dustpan principle made an improvement unavoidable. The single-roller throw-over principle - especially for larger sweepers - was developed to overcome these difficulties.
This further development in the world of sweeping technology opened the door to the future of efficient cleaning, but was by no means the last word in wisdom.
The problem of the roll-in/throw-out principle
The brush roller, which rotates anti-clockwise in the direction of travel, sweeps the debris that has passed the rubber lip (problem area I) overhead into the dirt container at the rear. This fills the hopper from above, which significantly increases the effective usable volume, but does not solve all problems.
Problem Area 1
A rubber skirt is still necessary to seal the sweeping area at the front and to prevent debris from being ejected forward. However, as with the single-roller dustpan principle, lighter materials are pushed ahead of the rubber skirt and cannot be collected by the sweeper.
Problem Area 2
If the roller brush becomes worn and its diameter is reduced, it no longer makes contact with the brush tunnel in the upper-right quadrant, rendering debris transport impossible. The maximum size of debris that can be collected is determined by a fundamental trade-off:
On the one hand, the skirt requires a certain level of stability and, therefore, a low height to prevent debris thrown against it from exiting the machine at the front. On the other hand, a taller rubber skirt is desirable to allow larger particles to pass underneath.
Tandem scooter system (TRS)
The solution for perfect sweeping results
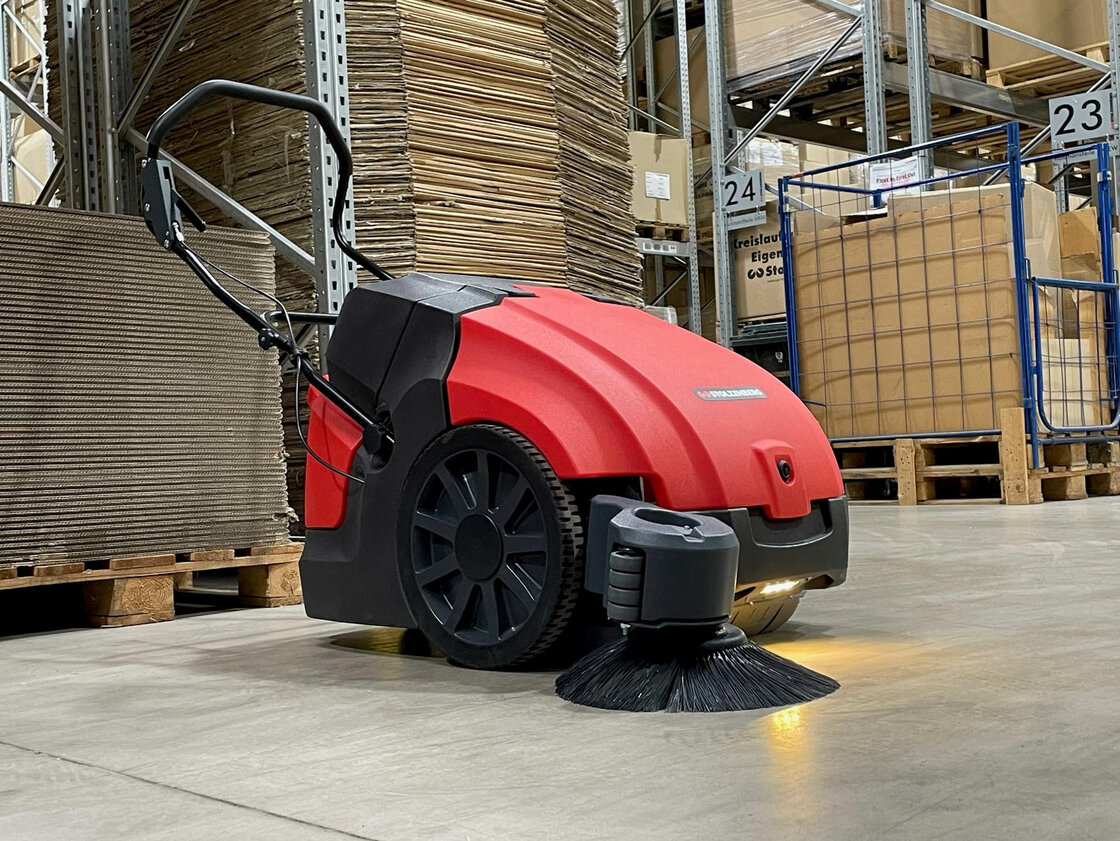
Inspired by these shortcomings, which have not yet been completely eliminated, a better sweeper technology was born over 30 years ago in our development department after a great deal of research: the tandem roller system (TRS).
The TRS has eliminated all the weaknesses of its predecessors and has virtually revolutionised the sweeper.
The pioneering functionality of the TRS
The two roller brushes rotate against each other - the front one with and the rear one against the direction of travel. The front roller brush works purely as a transport roller and therefore rotates in the air without making contact with the floor - so it is not subject to wear and requires little power.
The debris that has overflowed the front brush is fed to each other by both rollers and transported upwards.
A precisely defined guide plate above the intersection point of the rollers guides the dirt that is thrown upwards by the interaction of the rollers to the rear. In this way, it reaches the dirt container overhead.
One or two side brushes support the work of the roller brushes by sweeping debris from corners and edges in front of the roller brushes, which then pick it up.
All problem areas of the other sweeping principles no longer apply
Solution 1
All debris that fits under the core of the brush rollers is collected. The flexibility of the bristles allows objects up to the size of a bottle to be picked up, even with manual sweepers, while fine dust and sand are also reliably collected. There is no front-mounted dust container to cause blockages.
Solution 2
The absence of a rubber lip ensures that even lighter, bulkier objects, such as styrofoam and dry leaves, can be captured by the front roller brush and collected by the sweeper. Additionally, the slight vacuum created between the roller brushes allows the machine to effectively pick up challenging debris, such as flat-lying paper on the ground.
Solution 3
The waste container is filled from the top, ensuring optimal utilization of its volume. A height-adjustable sweeping roller compensates for wear and ensures the necessary sweeping depth is maintained, even on uneven surfaces.
Solution 4
In Stolzenberg's extensive range of sweeping machines, you will find the right TRS sweeper for your specific needs. And if you require a machine for particularly specialized tasks, we are happy to work with you to develop your very own customized solution.
The Stolzenberg vacuum sweeper
Less dust, even more cleanliness
The consistent use of sweepers generally achieves a higher level of cleanliness than time-consuming and labour-intensive broom cleaning. By extracting dust during the sweeping process, our vacuum sweepers clean effectively and sustainably, especially in areas with a high dust content.
The dust particles swept up from the floor enter the dust container with the whirled up air. To reduce this excess pressure - so that the dust does not escape from the machine in an uncontrolled manner - the air is drawn through the filter. In this way, only the fine dust enters the filter, which is simply cleaned from the outside: The dust trapped in the filter falls directly into the dust container.
This technology means that only the particles that belong there get into the filter: Fine dust. Paper and other larger particles go directly into the coarse dust container and cannot clog the filters.
The fine dust is therefore not whirled up and does not get back onto the surfaces to be cleaned. The suction mechanism is available for both electric sweepers and sweepers with combustion engines. Even the drive of the smallest vacuum sweeper has an output of more than 200 m³/h.
In some vacuum sweepers, this motor also serves as a stepless forward drive. The result is unrivalled ease of movement during cleaning operations.